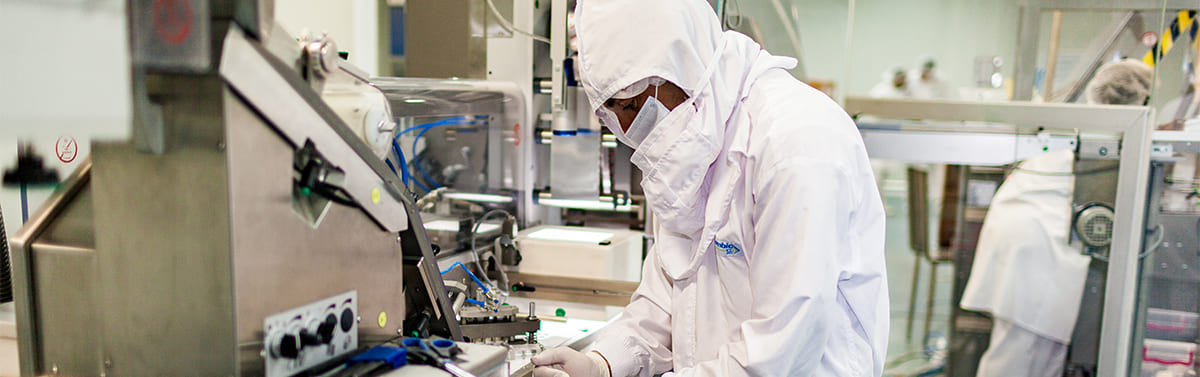
Automatización de procesos críticos de negocio
En el presente artículo analizaremos cómo la automatización de procesos permite controlar los procesos, generar información fiable para generar una trazabilidad robusta del producto y facilitar la toma de decisiones, así como la optimización de los procesos dependiendo en menor medida de los usuarios de planta.
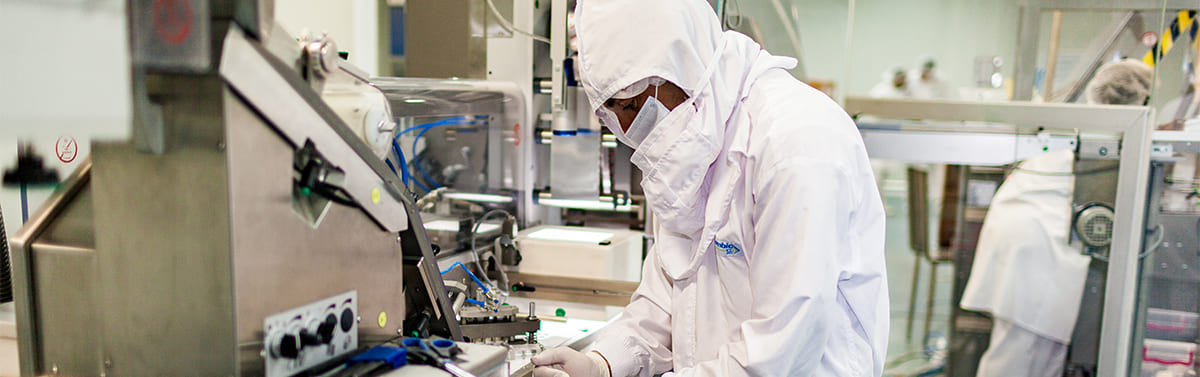
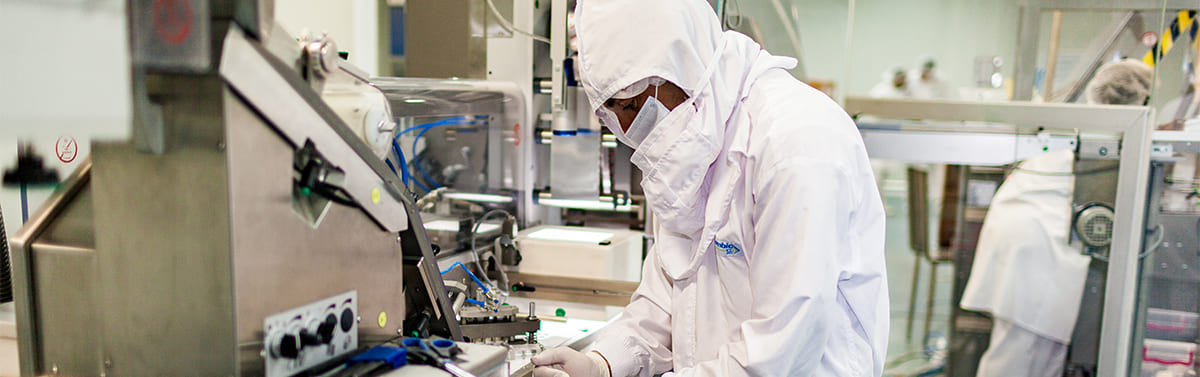
Principio GxP
Se debe considerar, cuando implantamos sistemas informatizados en sectores regulados como el farmacéutico o sanitario, la existencia de normativa aplicable a la verificación y mantenimiento de los sistemas informatizados. Dichas normas tienen como fin asegurar el uso previsto de los sistemas en todo su ciclo de vida, es decir, desde su adquisición o desarrollo, pasando por la verificación de su funcionamiento, aseguramiento en todo su tiempo de uso, hasta su retirada.
El anexo 11 de las normas de correcta fabricación de medicamentos, dedicado a los sistemas informatizados, determina como premisa que “cuando un sistema informatizado reemplace una operación manual, no debe ser en detrimento de la calidad del producto, control del proceso o garantía de calidad. No debe haber un incremento del riesgo total del proceso”.
Durante todo el proceso de automatización se debe tener en cuenta esta premisa. Una forma muy efectiva para su cumplimiento es tener siempre presente las necesidades del proceso a automatizar. Es decir, analizar previo a la adquisición o desarrollo de los sistemas a implantar, los requisitos funcionales, de seguridad o integridad de datos que el proceso requiere. De este modo se ofrecerá la cobertura prevista tanto a nivel de control de procesos como de trazabilidad.
Poniendo el foco en las características y requisitos de los procesos a automatizar y no en el funcionamiento estándar de los sistemas informatizados a implantar se asegurará parte del éxito del proyecto.
Objetivos de la automatización
A continuación, se analiza desde diferentes perspectivas los objetivos de la automatización:
Mejora continua
Una práctica muy extendida en la industria es el lean manufacturing. Esta metodología se basa en el conocimiento exhaustivo de los procesos, poniendo en foco en el conocimiento y experiencia de sus especialistas: las personas que los diseñan, ejecutan y controlan.
Con este conocimiento del proceso se diseñan acciones para eliminar riesgos del proceso, generar información certera y eliminar desperdicios (todo aquello que no genera valor).
Por tanto, el lean manufacturing, genera un entorno que busca constantemente la optimización y control de los procesos y la información de valor es el fundamento de esta estrategia. Un lema propio de esta metodología es “para mejorar primero hay que medir”.
Una de las formas para conseguir esta información de valor es mediante el uso de sistemas informatizados que controlen y registren los datos en tiempo real.
Aseguramiento de procesos
Hasta hace relativamente poco la industria controlaba sus procesos críticos a través de procedimientos que narraban de forma clara y precisa la gestión a realizar por los operarios involucrados y el registro requerido para dejar constancia de la ejecución y los valores de los parámetros críticos obtenidos en su transcurso. Esta gestión se ha considerado completa y correcta, no obstante, tiene riesgos intrínsecos a su diseño. Los principales riesgos de la gestión manual del proceso es la alta dependencia del operario en que ejecute las tareas en el momento, forma y calidad oportuna, así como el riesgo asociado al registro manual de los datos del proceso por parte del usuario.
Implantar sistemas informatizados para el control de los procesos críticos aporta las siguientes ventajas:
- Registro automático de la información y evitar, en la medida de lo posible, la introducción de datos manuales por parte del operario. Por ejemplo, registrar en tiempo real y de forma automatizada la fecha y hora, el operario que realiza la acción, el producto utilizado (por lectura de código de barras o similar), así como valores del proceso mediante la integración con equipos de proceso (como loteadoras de producción, básculas o climas) o instrumentos de laboratorio.
- Permite guiar al operario en sus tareas, para seguir los protocolos definidos y en vigor e introducir controles en proceso que eviten los errores. Un ejemplo de esta gestión es determinar la tarea a realizar por un operario de almacén, guiando al operario en la preparación de las materias de la orden más prioritaria según planificación y especificando hueco de almacén y bulto a preparar con el fin de optimizar sus movimientos. Esta gestión también permite evitar errores, por ejemplo, asegurando que el usuario ha preparado el lote de producto previsto mediante la solicitud de confirmación del bulto por lectura de código de barras.
- Representación de la información de forma automática. El registro automático del proceso permite explotar la información tanto para la toma de decisiones, como para dar soporte a los operarios que están ejecutando o monitorizando el proceso. Los gráficos de tratamiento de información agrupada en sala permiten observar tendencias que pueden dar soporte al usuario en el control del proceso, para evitar incidencias, así como monitorizar el cumplimiento de objetivos.
- Gestión de alertas y notificaciones.
La automatización de procesos de negocio críticos tiene cada día mayor peso entre las empresas del sector sanitario, farmacéutico, cosmético o alimentario
La gestión a tiempo real y automatizada del proceso permite enviar notificaciones a usuarios para informar que se han producido ciertos eventos en un contexto específico. Esta gestión puede permitir una optimización de tiempos muy importante, así como evitar incidencias de calidad del producto y evita la dependencia de los usuarios del proceso pudiéndose éstos concentrar al máximo en la gestión del propio proceso.
Cumplimiento normativo
La normativa aplicable a los sectores regulados es cada vez más exigente solicitando la ejecución de controles en proceso y registro de su evidencia. Esta exigencia finalmente se traslada al operario de planta, responsable de dejar registro de los valores del proceso, solicitándole la ejecución cada vez más frecuente de cálculos, en ocasiones muy complejos, que pueden aumentar el riesgo de error en el cálculo o registro del resultado, así como que el operario traslade su atención al cálculo y no al proceso que está monitorizando.
La automatización de procesos permite el procesamiento automático de datos evitando los errores humanos y teniendo la posibilidad de tener en cuenta un número más amplio de variables.
Explotación de datos
La gestión del proceso en papel permite registrar la información crítica para controlar el proceso GxP. Pero ante una incidencia o para tener una visión agrupada de lo ocurrido el acceso a esta información puede ser costosa en tiempo y forma, así como introducir ciertos riesgos.
La automatización de procesos permite el registro automatizado de las variables críticas. Este registro permite la explotación de la información para la toma de decisiones. Permite definir una estrategia de acción basada en datos. Así como analizar la información teniendo en cuenta diferentes perspectivas.
Riesgos de la automatización
Como se ha analizado en el punto anterior son numerosas las ventajas de la automatización de procesos, pero también tiene asociados riesgos que debemos destacar:
- Incumplimiento del funcionamiento previsto del sistema. Ejecución no controlada e insegura del sistema.
- Datos no fiables por la ausencia de medidas de control. En todo el ciclo de vida del dato desde su generación pasando por su selección, representación, procesamiento, almacenaje, recuperación, distribución, uso, archivo y destrucción.
- Gestión incorrecta del mantenimiento y/o configuración del sistema.
- La agrupación incorrecta de la información puede dar lugar a un valor y significado incorrecto del indicador.
Tipos de sistemas informatizados
Durante el proceso de automatización se puede hacer uso de diferentes tipos de sistemas informatizados que actúan a diferentes niveles o con diferente finalidad. En la Figura 1 se identifican estos niveles de gestión de proceso e información:
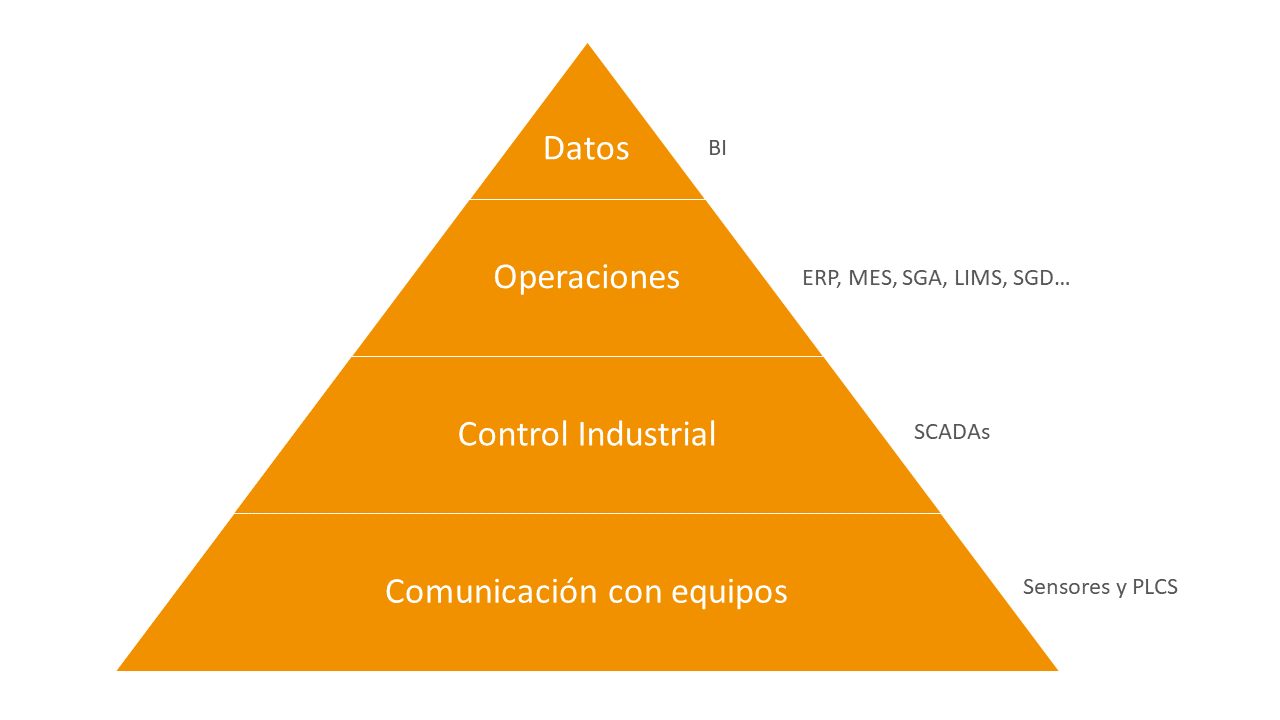
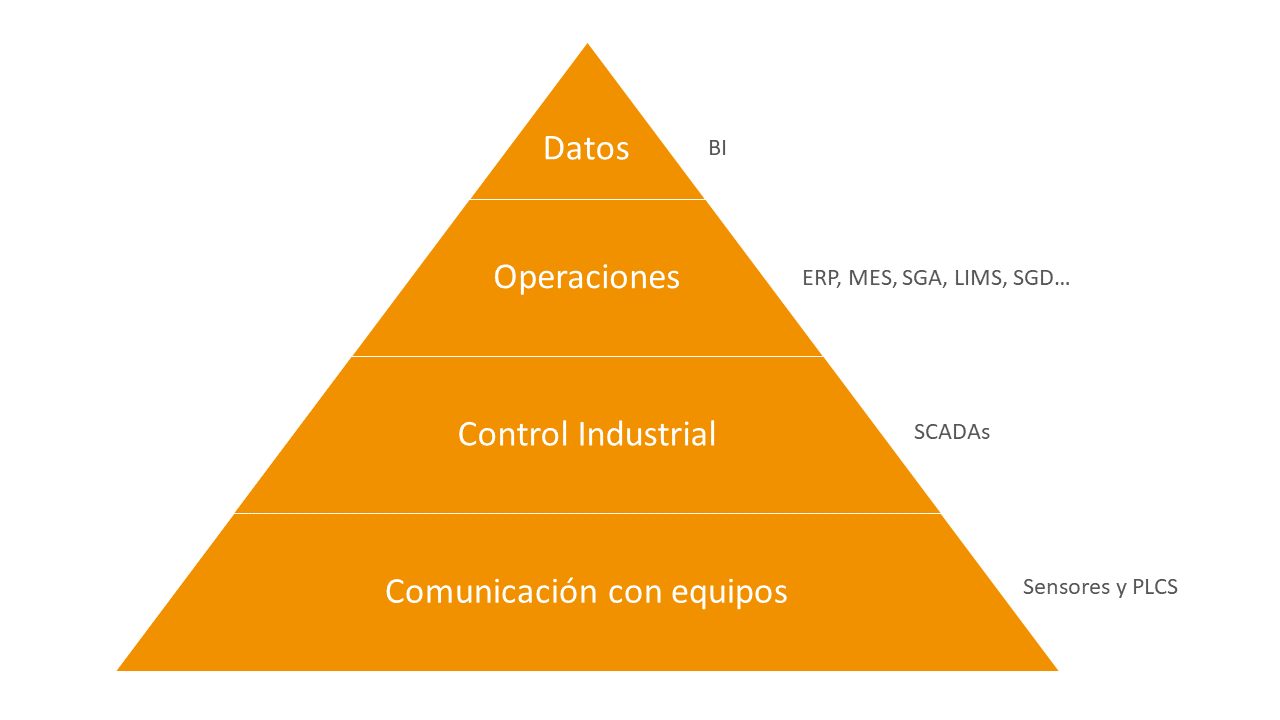
La primera capa de la pirámide, empezando por la base, hace referencia a sistemas informatizados, de muy bajo nivel, que son capaces de integrarse y comprender las señales del equipamiento físico/industrial de la planta.
La segunda capa hace referencia al control industrial. Estos sistemas permiten gobernar el equipamiento físico de planta y gestionar la intervención de los usuarios en el proceso.
La tercera capa hace referencia a las operaciones. A este nivel se pueden gestionar los procesos definidos y regulados, teniendo en cuenta la intervención de los usuarios, automatizando y controlando los procesos e integrándose con equipos para reducir la introducción de datos manuales.
La cuarta capa llamada datos permite explotar la información, dándole significado y permitiendo la toma de decisiones estratégicas por parte de la organización.
Objetivos a corto, medio y largo plazo
El objetivo de la automatización a corto plazo es controlar los procesos críticos de negocio utilizando el sistema informatizado por los usuarios finales como guía en el proceso y aplicando las medidas de control necesarias. Así como obtener los datos primarios del proceso en tiempo real.
A medio plazo la automatización permite disponer de un conjunto de datos procesados y fiables que tienen un significado (relevancia, propósito y contexto) y que, por lo tanto, son de utilidad para quién debe tomar decisiones, al disminuir su incertidumbre. A largo plazo, contemplando la información generada por el sistema y la experiencia y conocimiento de los usuarios sirve como marco para generación de un plan de acción estratégico basado en datos.
Estrategia de implantación de sistemas informatizados
Se debe prestar especial atención a la estrategia de automatización. Los objetivos finales deben estar marcados desde el principio, pero la forma del desarrollo del proyecto debe estar planificada y secuenciada de manera estratégica.
La automatización de procesos tiene múltiples ventajas, pero la resistencia al cambio en las organizaciones si no se gestiona de forma adecuada, puede ser un importante factor de riesgo para el desarrollo y éxito del proyecto.
La Figura 2 representa la cadena de valor de una empresa fabricante de medicamentos. La cadena de valor permite examinar y dividir la compañía en sus actividades estratégicas más relevantes. Se identifican dos tipos de áreas, las primarias y las de soporte:
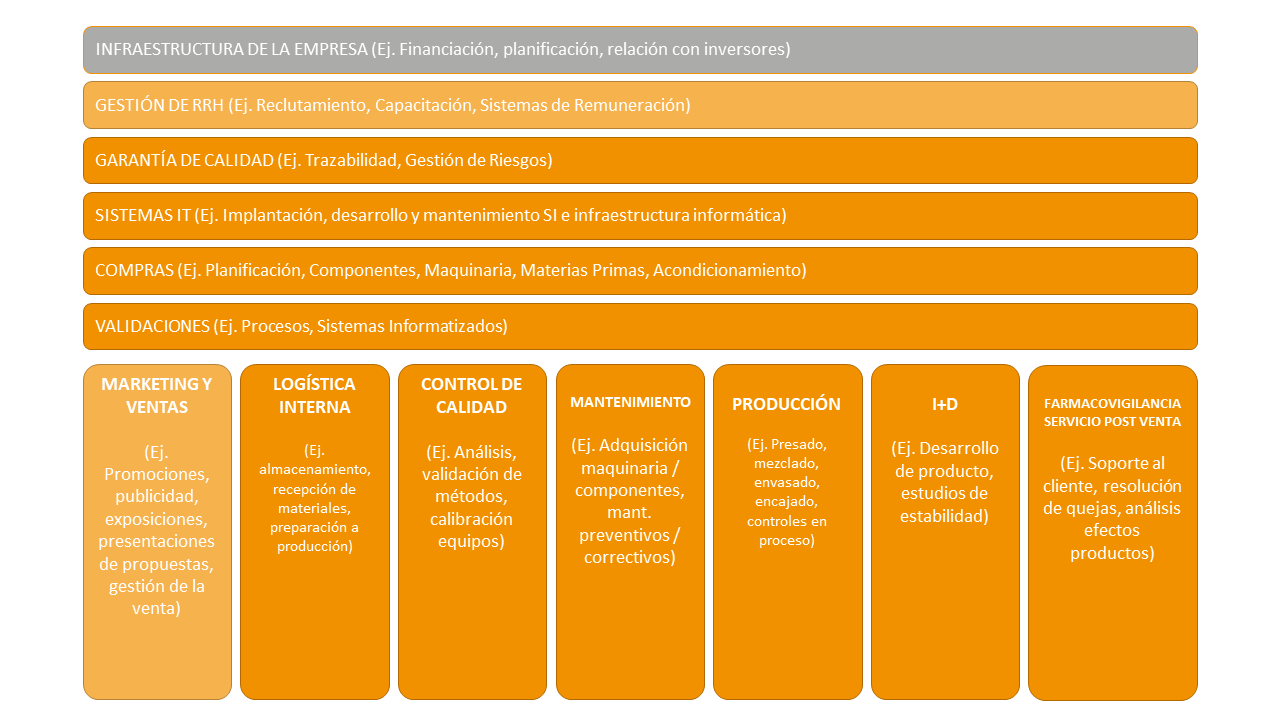
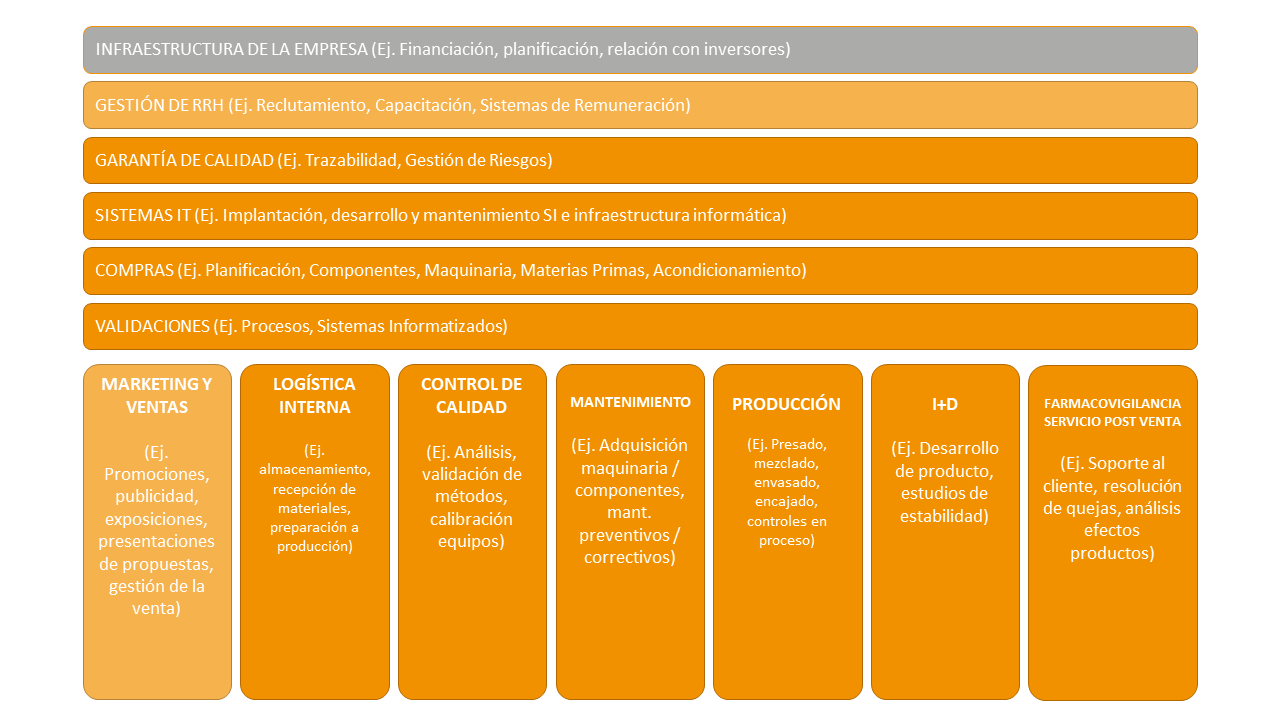
Las áreas primarias están enfocadas en la elaboración y/o control del producto y, aunque dependen del resto de áreas de la organización, gestionan de forma individual su proceso. Las principales áreas primarias identificadas son producción, logística, control de calidad, I+D o farmacovigilancia.
Como áreas soporte se pueden entender los departamentos que prestan servicios a las áreas primarias para su correcto desarrollo. Las principales áreas de soporte son calidad, IT, recursos humanos o compras.
Para representar la cadena de valor se ha utilizado un código de colores el cual nos identifica el grado de impacto GxP de las áreas representadas. El impacto GxP alto queda representado por el naranja, el impacto GxP medio por un naranja más claro y las áreas sin impacto GxP quedan representadas en gris.
La automatización completa de las áreas y la organización es posible, pero se aconseja que se diseñe un sistema escalable y se vayan ejecutando proyectos de digitalización de procesos concretos y controlados con la perspectiva del objetivo de digitalización completo.
El proceso de automatización podría ser el siguiente:
- Empezar por la implantación de la base de un ERP (sistema de planificación de recursos empresariales) para el control de los datos maestros (información sobre proveedores, clientes, artículos) y la gestión de forma administrativa de pedidos de compra, venta y generación de órdenes de producción. El uso de este sistema sería sencillo, pero nos aseguraríamos que es escalable a la hora de ampliar funcionalidades y que cuenta con las seguridades que nos requiere la normativa aplicable. Hasta este momento dispondríamos de formadigitalizada de la información base.
- A partir de este momento se aconsejaría continuar con un sistema de gestión de almacén. Para gestionar en tiempo real y en las instalaciones la entrada de mercancía, el bloqueo de calidad de las materias, el aprovisionamiento de materias a producción, el alta de producto fabricado y la expedición de los productos a clientes. Con este proyecto podríamos gestionar el stock de forma adecuada, así como controlar y registrar actividades críticas para la trazabilidad y calidad del producto.
- Los proyectos siguientes podrían ser la automatización de la fabricación, con un sistema MES, o la automatización del proceso de control de laboratorio con un sistema LIMS.
- Gestión de áreas soporte como la de mantenimiento, con la implantación de un sistema GMAO, que controle mantenimientos correctivos y preventivos de las máquinas de proceso y las instalaciones. Así como gestión de la documentación con la implantación de un sistema de gestión documental o SGD.
- Teniendo la información del stock, la logística interna, producción, análisis y mantenimiento, se podría implantar un planificador o MRP para optimizar los tiempos, capacidades de máquina y gestión del stock.
- Implantación de un business intelligence, BI, para la explotación de la información para el control de procesos, toma de decisiones y diseño de la estrategia empresarial.
El diseño de los sistemas informatizados a implantar dependerá de los requisitos y objetivos de digitalización de la compañía. En caso de que no se disponga de una gran complejidad de procesos se podría optar por seleccionar un sistema informatizado global que disponga de diferentes módulos para la gestión de los diferentes procesos, como pueda ser SAP o SAGE. O que se disponga de un ERP más básico y que se implanten sistemas informatizados especialistas en ciertas actividades, como un sistema de gestión de almacén, un sistema de gestión de laboratorio, un sistema de gestión documental, etc.
Tratamiento de la información
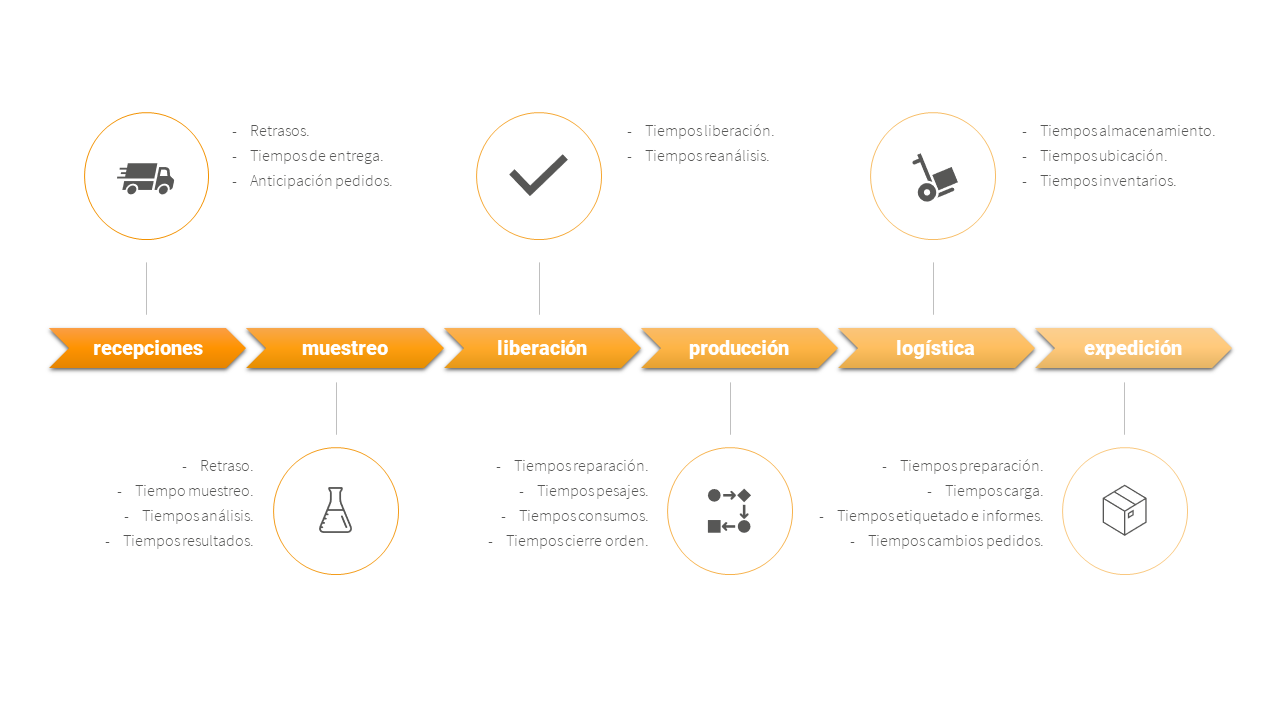
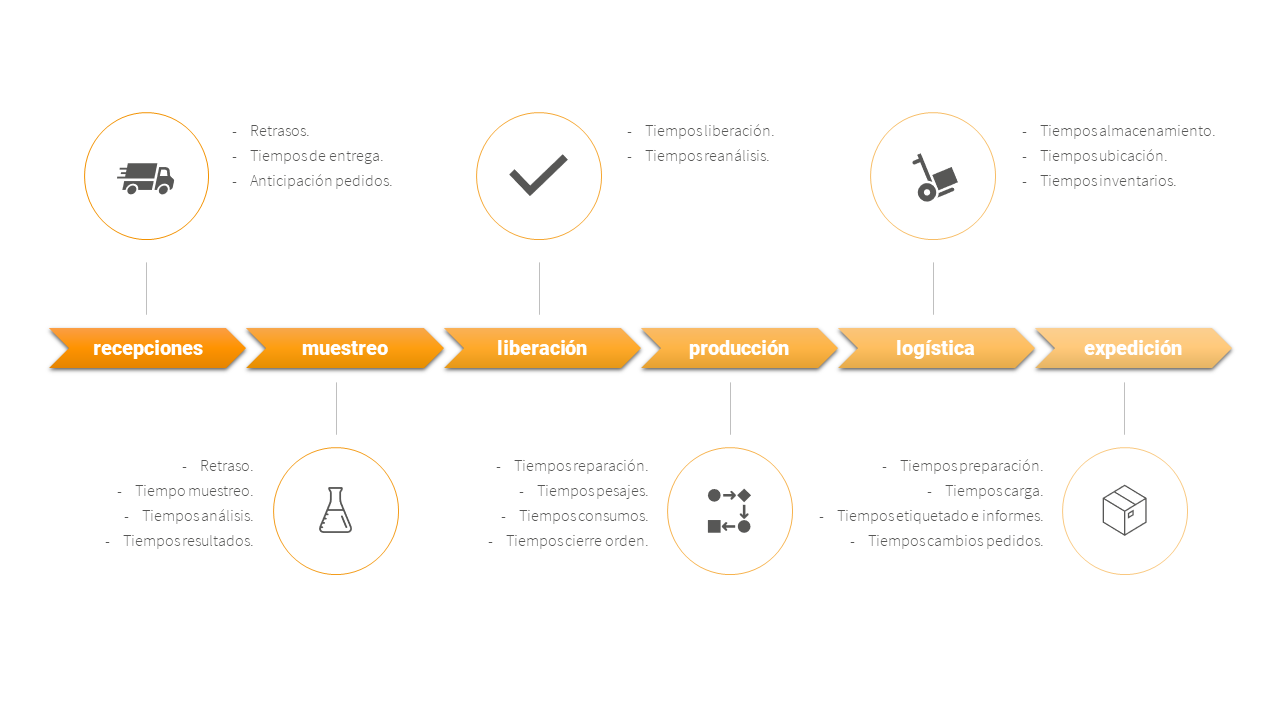
La Figura 3 representa cómo se puede explotar la información de una forma agrupada, poniendo un ejemplo de un estudio de control de tiempos de los procesos críticos de negocio de una empresa fabricante de medicamentos. Por fase del ciclo de vida de un producto se identifican tiempos a monitorizar. Por cada parámetro temporal de tiempo a medir se establece un tiempo óptimo y se compara con el tiempo real para determinar posibles desviaciones e investigar su causa raíz. De esta forma se pueden diseñar medidas correctivas y preventivas basadas en datos.
Conclusiones
- La automatización de procesos genera información fiable para la toma de decisión facilitando la ejecución de los procesos clave a los usuarios finales.
- La automatización se debe planificar de forma estratégica identificando los objetivos finales a conseguir, seleccionando los sistemas informatizados adecuados y realizando una implantación del cambio de forma escalonada para que sea digerible por la organización.
- La automatización además de permitir una correcta trazabilidad, permite explotar la información desde diferentes ángulos, lo que permite diseñar un plan de acción estratégica basado en datos.
Artículo originalmente publicado en la revista de Pharmatech, en el número 56 de Marzo-Abril 2021.
¿Necesitas asesoramiento personalizado para tu empresa? Contacta con nuestros consultores, sin compromiso, a través de nuestro correo info@oqotech.com o colombia@oqotech.com. Estaremos encantados de poder ayudarte.