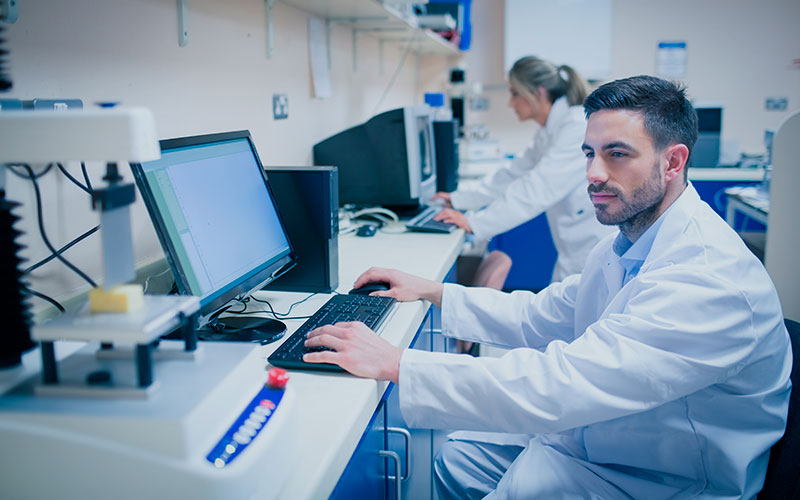
Common problems in corrective and preventive actions
We analyzed some problems in the process of corrective and preventive actions (CAPA) – an essential element of the quality system for medical devices – where a large number of observations from regulatory bodies occur.
The process of corrective and preventive action (CAPA) remains a major challenge for medical device manufacturers.
Regulatory bodies always evaluate the Corrective and Preventive Action Process (CAPA) in their inspections, hence the importance of identifying potential problems and implementing appropriate solutions.
Planning an effective approach to manage this process is key, and not only from a regulatory point of view, but also to ensure the processes and operations of the company.
For this reason, we have considered it particularly important to prepare and share this guide on the most common problems in the process of corrective and preventive action (CAPA).
What is the Corrective and Preventive Action Process (CAPA)?
There is a great deal of literature that defines the corrective and preventive action process (CAPA). However, for the medical device industry, an appropriate definition is included in ISO 13485, in clauses 8.5.2 Corrective Action and 8.5.3 Preventive Action:
8.5.2 Corrective Action
The organization must take steps to eliminate the cause of the nonconformities in order to prevent a recurrence. Any necessary corrective action shall be taken without undue delay. Corrective action shall be proportionate to the effects of the nonconformities found.
The organization must document a procedure to define the requirements for:
- Reviewing nonconformities (including complaints)
- Determine the causes of the nonconformities
- Assess the need for action to ensure that nonconformities are not repeated
- Plan and document the necessary actions and implement those actions, including, as appropriate, updating documentation
- Verify that the corrective action does not adversely affect the ability to comply with applicable regulatory requirements or the safety and performance for the medical device
- Review the effectiveness of the corrective actions taken
- Maintain records of the results of any investigation and action taken (expand with section 4.2.5)
8.5.3 Preventive Action
The organization must determine actions to eliminate the causes of potential nonconformities in order to prevent them from occurring. Preventive actions shall be proportional to the effects of potential problems.
The organization shall document a procedure to describe the requirements for:
- Determine potential non-conformities and their causes
- Assess the need for action to prevent the occurrence of nonconformities
- Plan and document the necessary actions and implement those actions, including, as appropriate, updating documentation
- Verify that the action does not adversely affect the ability to comply with applicable regulatory requirements or the safety and performance of the medical device
- Review the effectiveness of preventive actions taken, as appropriate
- Maintain records of the results of any investigation and action taken (expand with section 4.2.5)
This implies meeting the following requirements:
- Analyzing processes and documents that may reveal non-conforming products and other sources of quality problems.
- Investigate the root cause of these found nonconformities.
- Define the necessary actions to prevent and correct recurrence.
- Verify the efficiency and effectiveness of these actions.
- Present relevant reports on the quality problems identified and the corrective actions proposed.
- Identify process and procedures that require modification in order to correct or prevent quality problems, and record these changes in a timely manner.
- Ensure that information on quality problems is presented clearly and timely to the company’s management.
Common problems in the process of corrective and preventive actions (CAPA)
Some of the main problems that medical device companies encounter when implementing corrective and preventive action processes (CAPA) are:
Responsibility for the process
CAPA is a topic that is usually assigned to the quality team in the organization. This means that problems are not dealt with from a global perspective, and important information can be overlooked. In addition, reviews of CAPA actions tent to be conducted with a regular meeting, which in some organizations is usually held every six months, if not annually.
The process of corrective and preventive actions (CAPA) should be treated as a project of interest to the organization. It should be the responsibility of a multifunctional and multidisciplinary team, involving key employees from various areas. It should be called at the earliest possible moment of warning of problems, at least once or twice a month.
The process’ approach
In the quality management environment, organizations of all kinds have become accustomed to being reactive. The ability to respond immediately to the appearance of compliance problems or compliant is considered to represent a large part of the effectiveness of the quality area.
But what if we don’t wait for non-conformity, but think about it from the beginning of the production process? And what if we don’t wait for the client to report a non-conformity and go in search of it, asking, polling, investigating?
This is certainly a different approach. A proactive approach based on the course on CAPA and that is a further step in addressing it.
Deficiencies in determining the root cause
This happens when CAPA is set in motion without due to attention to identifying the root cause. Some practitioners reduce the problem to a semantic aspect: they pose the problem with other terms, without getting close to the origin.
Thus, the possibility of recurrence is assured. There are many methods to determine the root cause. The method of the 5 why’s is perhaps one of the most used, but sometimes it does not take into account that it does not necessarily have to be 5. Some problems may go up to 10, while in others the correct answer may appear in the number 3.
Disproportionate use of CAPA
When we talk about disproportionate use, we are not just talking about excessive use. It also includes little or no use of it when it is necessary. The key is to understand that the process of corrective and preventive actions (CAPA) must be applied when a systemic problem occurs or may occur. And not all complaints are of this type.
If a CAPA is declared for every complaint or grievance, however small and insignificant it may be, and especially when it is a temporary event, the system is overloaded. And so, the functionality of the CAPA is diluted and in many cases, the solution acquires a higher cost than the problem being addressed.
Correcting these issues brings quality laboratories of companies in highly regulated sectors closer to correctly complying with their process of corrective and preventive actions (CAPA) and avoiding calls for attention from regulatory bodies.
At Oqotech, we are highly experienced professionals in the sector. If you need support to define your corrective and preventive action process, contact our team and receive help to face this process successfully.